Bell: Difference between revisions
Ksgallagher (talk | contribs) |
Ksgallagher (talk | contribs) |
||
(2 intermediate revisions by the same user not shown) | |||
Line 32: | Line 32: | ||
===Anatomy and Tuning of a Bell=== | ===Anatomy and Tuning of a Bell=== | ||
The basic anatomy of a bell is fairly universal. On the top of the bell there is typically a wooden crossbeam called a yoke that the bell is attached to. The connecting piece is known as the crown. Commonly made of metal, the crown can be directly attached to the yoke, or the bell can dangle with the crown being tied to a series of leather straps. Connected to the crown of the bell is the head and shoulder section of the bell. This section is tuned to resonate one octave higher than the hum, or main note. The main section of the bell is referred to as the waist. This is the largest section of the bell and is tuned to resonate at a fifth, or quint, of the hum tone. The bottom section of the bell where the flare begins is known as the sound bow. This section is attached to the lip, the very bottom of the bell, and is responsible for the generation of the hum tone. The open bottom of the bell is the mouth. Within the mouth of the bell can be seen the clapper, which is usually a metal rod attached to a metal ball. The clapper hangs free from the shell of the bell so as to invoke independent movements. | The basic anatomy of a bell is fairly universal. On the top of the bell there is typically a wooden crossbeam called a yoke that the bell is attached to. The connecting piece is known as the crown. Commonly made of metal, the crown can be directly attached to the yoke, or the bell can dangle with the crown being tied to a series of leather straps. Connected to the crown of the bell is the head and shoulder section of the bell. This section is tuned to resonate one octave higher than the hum, or main note. The main section of the bell is referred to as the waist. This is the largest section of the bell and is tuned to resonate at a fifth, or quint, of the hum tone. The bottom section of the bell where the flare begins is known as the sound bow. This section is attached to the lip, the very bottom of the bell, and is responsible for the generation of the hum tone. The open bottom of the bell is the mouth. Within the mouth of the bell can be seen the clapper, which is usually a metal rod attached to a metal ball. The clapper hangs free from the shell of the bell so as to invoke independent movements. | ||
''For more information on bell ringing, see [[Bell]]'' | |||
''For more information on bell ringing, see [[Bell]] | <br /> | ||
[[File:PartsOfABell.jpg|400px||center| Bell Anatomy ]] | [[File:PartsOfABell.jpg|400px||center| Bell Anatomy ]] | ||
Latest revision as of 10:16, 2 December 2015
This page is a description of a typical Venetian bell. For an overview of all the bells in Venice, see Bells.
A Venetian bell, known in Italian as campana, has had many different uses. Before modern times, bells had more purpose than pure musical entertainment. They were signals of danger, disaster, and alarm. Many bells of today were built in medieval times, and were manufactured using a specific set of techniques and materials.
Bell Construction
The casting of bells is a delicate and precise process. The style of a particular bell depends upon the foundry in which it was made, along with the materials that compose it and the period of its creation.
Material of Bells
The most common material for bells is bronze, an alloy of copper and tin. Very rarely bells were cast in steel and cast iron. This shift in bell materials occurred mainly during times of war, when alloys such as bronze were in short supply since copper was needed in the manufacturing of some weapons. Around 1857 A.D. a combination of iron and carbon, also known as steel, became a material for bell-making. Not soon after it had begun being used it was discarded since the compound was deemed unsuitable for a material of bells.
Bell Casting and Founding
Bells have typically been made using the same process for over six centuries. A popular method of bell casting is to use sand-casting. In medieval times, when many bells were being produced, molds were made from clay to make a template for the bells. A bell mold had a center mold and an outer mold, where molten bronze was poured between the two and then allowed to cool to take the shape of a bell. Back in the middle ages, sometimes wooden templates were also used. Through the use of these templates the distinctive shape of the bells was formed.
For more information about bell founding, see external_LINK.
Acoustics of Bells
Bells like any other sound generating device can be broken down to a science. The frequency of the waves and thus the sound generated by the vibration is directly proportional to the diameter of the bell and the thickness of the metal. Bells are made to exact formulas so when a diameter is chosen, it is possible to calculate every remaining dimension of the bell and its musical note or tone. The frequency of a bell's note varies with the square of its thickness, and inversely with its diameter.
If the bell is mounted as cast, it is called a maiden bell. Tuned bells are worked after casting to produce a precise note. The bell's strongest overtones are tuned to be at octave intervals below the nominal note, but other notes also need to be brought into their proper relationship. Bells are usually tuned via tuning forks or by more modern electronic tuners.
Striking Methods
Another key factor in the ringing of the bell is how they are struck. The first method often portrayed in movies is the swinging method. Usually a rope is tugged from the ground that causes the entire bell structure to swing back and forth, and inside the bell, a clapper strikes the sides causing vibrations as seen below. This method is not advisable as it causes a great deal of bell movement, and over time this motion can damage the support structure and leave a streak mark formed by the clapper if the bell is not balanced. The other method is striking the shell of the bell. This causes less structural damage, but over time can leave dents which might ultimately deform the bell and alter its sound. The last common method, similar to the hammer method, is to swing the clapper while the bell remains stationary.
Bell Frame Design
Two bell frame types are primarily used to suspend bells, the H frame and the A frame. The H frame occurs when the bell is suspended on a cross bar made of heavy H castings usually composed of a durable metal material such as cast iron. Alternatively, H-frames can be stand-alone parallel legs with a single cross beam that holds the bell. A-frames are metal structures that form the shape of an “A” and attach the bell to the ground of the belfry as seen below The metal material resists twisting and provides a secure base for the bell. The popularity of this type of design resides in its greater convenience and construction. The last method of attaching a bell is to mount it to a circular support structure that is free to rotate. The structure is then rocked back and forth while the bell is held firmly on the wheel.
Example of an H Frame:
Example of an A Frame:
Anatomy and Tuning of a Bell
The basic anatomy of a bell is fairly universal. On the top of the bell there is typically a wooden crossbeam called a yoke that the bell is attached to. The connecting piece is known as the crown. Commonly made of metal, the crown can be directly attached to the yoke, or the bell can dangle with the crown being tied to a series of leather straps. Connected to the crown of the bell is the head and shoulder section of the bell. This section is tuned to resonate one octave higher than the hum, or main note. The main section of the bell is referred to as the waist. This is the largest section of the bell and is tuned to resonate at a fifth, or quint, of the hum tone. The bottom section of the bell where the flare begins is known as the sound bow. This section is attached to the lip, the very bottom of the bell, and is responsible for the generation of the hum tone. The open bottom of the bell is the mouth. Within the mouth of the bell can be seen the clapper, which is usually a metal rod attached to a metal ball. The clapper hangs free from the shell of the bell so as to invoke independent movements.
For more information on bell ringing, see Bell
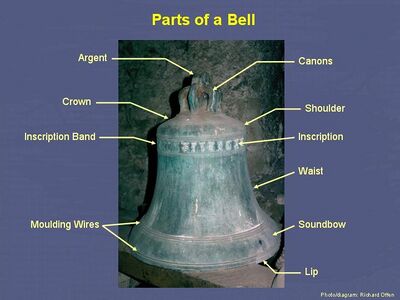
Bell Decoration
When ancient bells were cast, the moldings and decor on them were treated as a form of art. The inscriptions, figures, and design on each bell were well thought out by the founder and were intended to be a reflection of the founders work.
Most European bells are similar in their decorations, which usually include an inscription about where or when they were made or an engraving of a religious figure. Another trend founders have implemented was to design a trademark with a symbol or initials instead of writing out the full name of the founder.
Historical figures are a common form of art found on bells. These include effigies of saints, angels, or royal leaders. In addition, one may find the shield of the patron who invested in the tower or church. However, the most frequently used decor were inscriptions which offer information of whom the bell was dedicated to, who the maker or donor was, when it was cast, and other supplemental information. These are typically in Latin, although some may be in the native Italian.
IMAGES with examples
Bronze Corrosion
Most of the bells in Venice, being made of bronze, suffer from a cyclic degrading process known as Bronze disease. The disease refers to a chemical process in which the copper in bronze reacts with elements and moisture in the atmosphere creating a film signifying corrosion. Bell towers provide perfect conditions for bronze disease to propagate by leaving bells exposed to environmental conditions such as humidity, high winds, rain, and moisture. The thick green coating has the ability to transform the object by corroding the surface and possibly removing valuable artwork from its face. Many of the bells have intricate images exuding from their surfaces making corrosion a significant problem.
For more information on bronze corrosion, see external_LINK.
See Also
References